Our Technology
Modular Glulam Beam Technology
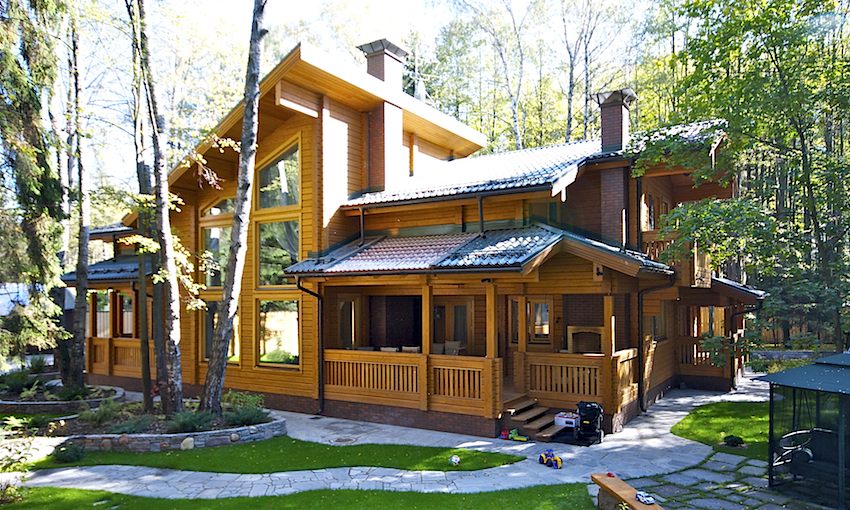
![]() |
![]() |
This technology is based on a modular system that cannot be matched by any of the company's competitors as it allows high-precision cutting and grooving of beam elements. With its specially developed program for designing houses built of beams the company is able to fully exploit the enormous potential. The resultant design (project) provides detailed and comprehensive design documents for the construction of a house. In 2006, we completed extensive modernization of its existing plant for the production of houses of glulam and solid beams.
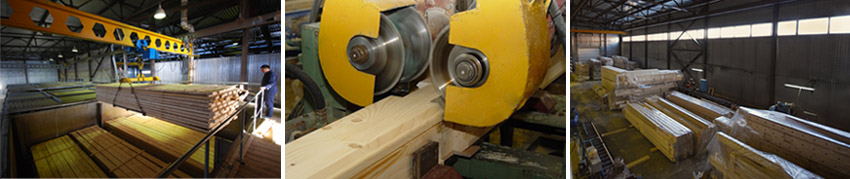
1. Material
Spruce vs. Pine
Based on many years of practical experience in the area of wood processing and house kit manufacturing, the company has ultimately chosen SPRUCE from the northern regions of the Russian Federation namely for the following reasons:
- SPRUCE is the most suitable of all coniferous trees - SPRUCE wood has an even white colour - SPRUCE wood has no large knots - SPRUCE wood has a low resin content - SPRUCE wood allows the possibility of replacing decomposed or rotten knots with healthy ones
We uses only whole spruce laminas (boards) for the production of glulam beams. Apart from providing a house built from such beams with an attractive exterior appearance, an even structure over the entire wall length is preserved and sharp or recurring changes in the beam body colour, which are so typical of pine wood, are eliminated.
We does not use pine wood, because large knots in the wood require the cutting of whole lamina sections and their subsequent rejoining lengthwise, which results in sharp changes in colour and visible joints on the body of the glued laminated beam.
Comparison of Spruce and Pine
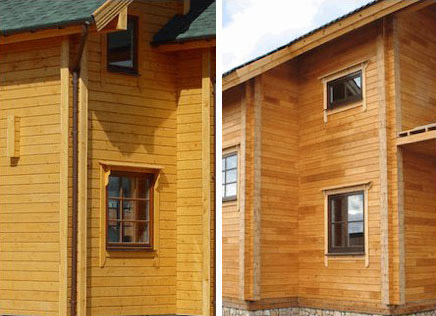
Finally, combining different types of wood in a beam increases the risk of its disintegration.
2. House Kit
Beam Set
A glulam beam house visualised virtually with the aid of powerful graphic design software is the exact copy of the house assembly subsequently manufactured at the plant and assembled at the construction site.
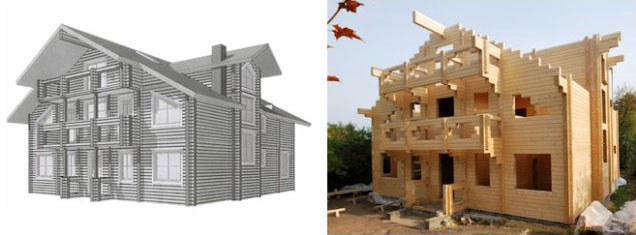
Building a House
The individual beam elements are manufactured on the grooving line precisely according to the project. The beams have circumferential grooves, front grooves for the installation of window and door units, as well as vertical grooves for the installation of wood screws, clamps and electrical wiring or sanitary mains. They eliminate the necessity of cutting additional grooves into the walls and enable to plan electric wiring and other communication networks during the design phase of the house.
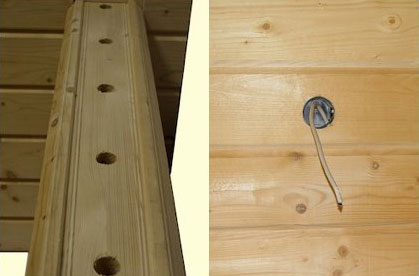
Additional Set:
![]() |
![]() |
![]() |
Butt plate (board): it serves for connecting 2 beam elements lengthwise inside the ring groove. | Metal components: M12 connecting pieces, plates (bearing), nuts and couplings; they are designated for the actual erection of the house on site. | Wooden screw (binder plug): a wooden birch baulk (28х28х330) intended for increasing vertical wall stability and reinforcing window and door openings. |
![]() |
![]() |
![]() |
PPE sealing: a reinforcement separator made of polyethylene foam, which is used for sealing the joints between ring beams. (It may be replaced by a band of ISOLENA sheep wool.) | Trimmed joints: wooden glued components with a cross-section of 59х254 mm, which serve as supporting members for floor and interfloor ceiling structures. | Fastening of trimmed joints: metal elements, with which the trimmed joints are fastened to walls. |
![]() |
![]() |
![]() |
Roof frame: wooden glued components with a cross-section of 59 х 254 mm, which serve as supporting members of the roof construction. | Fastening of truss: metal elements, with which roof beams are fastened together at the ridge beam. | Sliding support for truss: a fastening member used to ensure the free sliding of roof beams along walls. |
![]() |
![]() |
![]() |
Supporting column: a wooden glued laminated rectangular beam, which is used to increase the bearing capacity of ceilings. | Compensator: a metal device (a hoist) designated for regulating the gap between the supporting column and the ceiling crossbeam after the completion of the house assembly. | T-shaped base plate: it is used to install door and window frames and it also secures vertical movement with respect to walls. |
3. House Kit Assembly
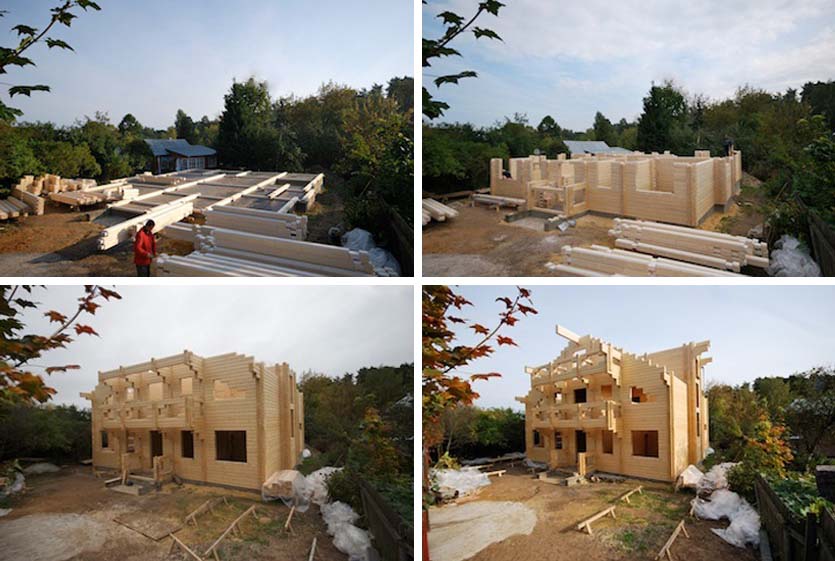
The erection of this house is fast and always with a quality result thanks to the modular technology and the wooden components that are manufactured with high precision and prepared for easy assembly directly at production plant.
Wood Protection
In order to protect the individual log house components, we use natural oils and waxes, which preserve the natural appearance of wood and enhance its weatherproof properties. Pigmented glazes by Kreidezeit, which are available in a wide range of colours and shades, add a special touch to the final look of the wood, as well as the individual components. The priming (ground) coat is applied when the log house is disassembled while still at the plant. The first coat protects the individual house components during transport. It is only temporary as it vaporizes after 2 months and a new coat providing long-term protection needs to be applied. The most suitable are natural oils and waxes because they provide wood with the necessary protection. These products offer comprehensive care for the interior and exterior of the log house.
Insulation
As regards insulation material in the houses built by us, clients may choose products from the ISOLENA company, which manufactures thermal insulation with the use of sheep wool. Sheep wool may replace all thermal insulation materials used throughout the house. Its thermal and insulation properties match other traditional insulation materials. As a genuinely natural material, sheep wool is becoming widely used in the construction of wooden houses. Thanks to its unique protein fibre structure, sheep wool creates a more pleasant environment inside the house. And since it does not contain any artificial or cellulose fibres, there is no risk of any dust or small particles being released into the air (as in the case of glass silk). Sheep wool insulation does not increase the volume of dust in the house either during installation or subsequent use. Prior to use, wool is treated with chemicals that enhance its resistance to pests and moisture. Naturally, wool is anti allergic and helps regulate the level of humidity in the interior. We recommend ISOLENA for the insulation of our wooden houses because it is an environmentally friendly and very pleasant material.
Wood is highly aesthetic, elegant and above all ecological. It is the healthiest and the most natural material for man.
Green Roof Technology
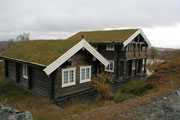
The most significant advantages include:
- Improved thermal and insulating properties of the roof construction
- Improved fire resistance
- Improved noise absorption
- Prolonged hydro insulation durability
- Water retention and gradual vaporization improves the microclimate of the structure surroundings
- Reduced day and night temperature fluctuations
- Beneficial impact on the surrounding environment
Green roofs are divided into two categories: extensive and intensive. Intensive green roofs offer the possibility of being used as an additional, grass-covered part of the garden. An intensive green roof is designed to accommodate people who may sunbathe or relax on it all day. Extensive roofs, on the other hand, are not designed to be walked on.
Parameters:
- Extensive roof:
80 – 170 kg/m2 roof construction load for 80 – 150 mm layers; various types of grass, moss and alpine plant species may be planted depending on the specific layer thickness
- Intensive roof:
300 kg/m2 and more roof construction load for layers from 250 mm (depending on the construction type and client requirements); various types of grass, smaller and larger tree and shrub species may be planted in the layer.
Intensive green roofs are fitted with safety railing. The inclination of green roofs ranges from 5 to 45° or even 90° in exceptional cases. For these types of roofs, we offer irrigation systems, as well as a wide variety of grass seeds, brush and other plant species.